SPP 2187 - Adaptive modularized constructions made in a flux: precise and rapid building
Complex bridge structures assembled by utilising facetted planar elements made of carbon-reinforced ultra-high performance concrete - Graph-based modularisation and trajectory-sensitive production
Projektbearbeitung: | Benedict Harder, Sebastian Esser, André Borrmann |
Förderung: | Deutsche Forschungsgemeinschaft (DFG) |
Zeitrahmen: | Phase 1 04/2020 - 03/2023, Phase 2 03/2023 - 03/2026 |
Partner: | TUM Chair of Concrete Structures |
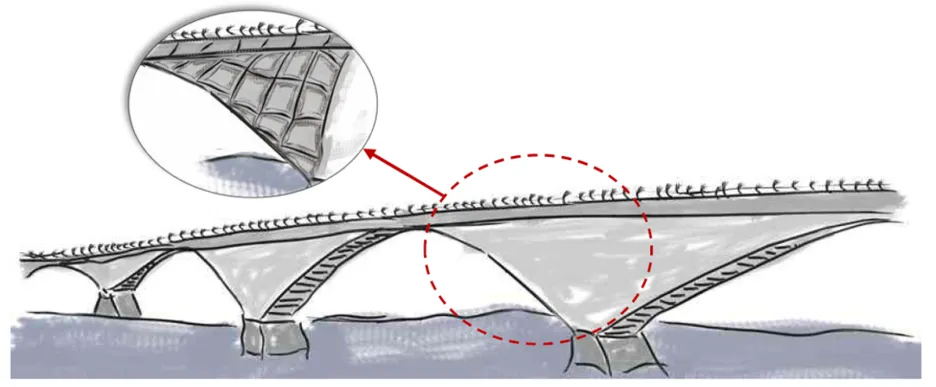
The basic idea of the research project is to further develop the modularization principle by using faceted structural elements made of carbon reinforced ultra-high performance concrete for concrete bridge construction. The approach, comparable to the geometrical division of load-bearing structures into finite elements, is characterized by the systematic decomposition of the overall structure into modules that are easy to manufacture. The boundary conditions to be observed here result on the one hand from structural-mechanical properties (load and component resistance, especially in the module joints), and on the other hand from the requirements of manufacture (module size and geometrical shape, manufacturing tolerances) and the subsequent assembly. The complex optimization problem ("optimal" module decomposition taking into account internal stress fields, production/assembly and the achievement of the highest possible degree of repetition) can only be solved by further development of computer-aided methods and the design of suitable modules, their joining technology and production.
In conventional concrete structures, joints represent complex discontinuity points, which usually entail elaborate individual detailed solutions and must be regarded as weak points with regard to the durability of the structure. Therefore, the quantity of joints is reduced to a minimum. A paradigm shift must be implemented in the entire building industry. The use of novel high-performance materials (e.g. ultra-high strength concrete with corrosion-free carbon reinforcement), an optimized joint arrangement and geometry as well as high-precision industrial production and suitable finishing and joining techniques can help to avoid previous disadvantages at the joints and, by means of a systematic modular design with facetted individual modules, to produce efficient and durable overall structures comparable to prefabricated segmental segments in highly segmented mechanical tunnel construction.
At the beginning of the segmentation or module form finding there is always a bridge geometry specified by the engineer. Thus, the method to be developed here should not be limited to conventional designs, but should also be fundamentally applicable to structures that are characterized by free geometric shapes. The decomposition of the initial geometry into modules shall be done by using a rule-based graph replacement system. This system is to function as a graph grammar and thus generate different variants for the decomposition into modules, which are then evaluated for their static suitability. The graph replacement system formally shows which module types can be used with which variability. Thus, the module form finding process is subject to the above-mentioned variability restrictions right from the start.
The different module types/forms and their possible degrees of freedom/restrictions regarding variability are represented by nodes and edges of a graph and are formally defined in a corresponding graph metamodel. Furthermore, graph substitution rules are formulated, which build a graph based on the metamodel, which describes the arrangement of the modules and their concrete forms (within the scope of the permissible variability). If these rules are used as productions of a graph grammar, a multitude of valid module arrangements can be automatically generated.