Additive Manufacturing in Construction - The Challenge of Large Scale
Project team leader | Dr.-Ing. habil. Stefan Kollmannsberger (TUM), Prof. Dr. rer.nat. Ernst Rank (TUM) |
PhD student | Oguz Oztoprak, MSc. |
Parent Research Project | The Transregio (TRR 277) |
Project | C01 Bridging Scales - From Geometric Part Details to Construction Elements |
Funding | German Research Foundation (DFG) |
Initial Running period | 01.2020 - 12.2023 |
Project overview
The Collaborative Research Centre TRR 277
The proposed Collaborative Research Centre TRR 277 Additive Manufacturing in Construction (AMC) – The Challenge of Large Scale intends to investigate new, digital additive manufacturing technologies in construction through holistic interdisciplinary research. The aim of TRR 277 is to create the basic conditions for the introduction of additive manufacturing in construction, and thus to pave the way for the use of resource-efficient constructions with a high level of design freedom.
C01- Bridging Scales
One of the most important advantages of additive manufacturing (AM) is the extensive geometric freedom in the design of parts. For example, additive manufactured steel nodes offer new opportunities for an individualised design of frame structures, and façade elements can be given unprecedented physical properties by means of printed mesoscale structures e.g.concerning translucence, thermal insulation etc. Another type of functional integration will also generate parts of locally varying properties by grading and inclusion of multi-materials in parts composed of minerals or steel. Common to all these examples is the multiscale nature of the structure. Properties of local components interact with the global behaviour of the construction. The geometric versatility – complex and diverse geometry of individual parts in constructions of virtually any shape – poses challenging expectations to numerical analysis software. In principle, an entire structure composed of all detailed parts could be analysed by one spatially resolved finite element computation. Yet, such a model might lead to tens of millions of degrees of freedom, and be completely unfeasible for a structural analysis. Therefore, a dimensionally reduced view is necessary for a global computation: Steel nodes, as an example, must be described by a few mechanical parameters only, while façade panels have to be characterised by homogenised thermal and mechanical properties as well. The individuality of AM parts enforces a numerical computation to extract these parameters themselves.
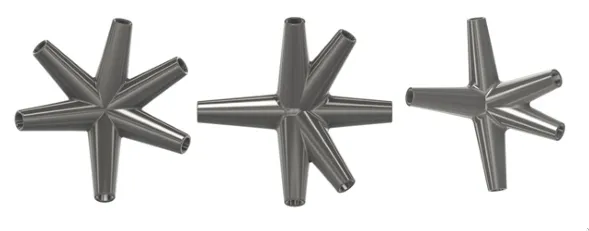
The goal of this project is therefore to develop a simulation technique that is able to directly couple the CAD design of AM parts to the building scale and their use in constructions. More specifically, the project, concentrating on product scales, has two closely connected central objectives: The first one is to develop – together with our partners – a consistent description for the relevant geometric models. The second focuses on efficient and effective mechanical simulation methods for AM products in construction, based on the multi-scalar geometric models. Two types of materials and corresponding processes will be in the centre of investigation in the first funding period, focusing on metal and concrete-based AM.
References
- Proposal for the Establishment and Funding of a Collaborative Research Centre TRR 277, Additive Manufacturing in Construction - The Challenge of Large Scale.