Overview
Ongoing research projects:
- AiF-DASt 22244 N/1 - Seal-welded hollow boxes
- DFG 506471463 - Method for assessing the remaining service life and determining safe operating time intervals of existing welded steel bridges
- AiF IGF 22741 N/2 - Modular rolled girder in concrete frame bridge
- DFG ME 3296/11-1 - Fatigue strength of the shear bond with headed studs under uniaxial and multiaxial fatigue loading based on reliability considerations
Completed research projects:
- AiF FOSTA 04267/17 - Galvanization-compliant design of integral frame bridges with medium spans with production-compliant joining using high-performance grouting mortar
- AiF DASt 20455 N/2 - Longitudinally stiffened buckling fields under multiaxial loading
- AIF 14771 N1 - Development and preparation of economic design rules for steel and composite beams with slender web plates in building and bridge construction
- AIF Zutech - FOSTA P 843 - Holistic evaluation of steel and composite bridges according to sustainability criteria
Fatigue strength of the shear bond with headed studs under uniaxial and multiaxial fatigue loading based on reliability considerations
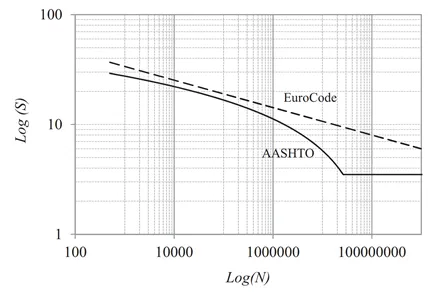
Source: OVUOBA, B., PRINZ, G. S.: Fatigue Capacity of Headed Shear Studs in Composite Bridge Girders. Journal of Bridge Engineering, 2016
- DFG project: ME 3296/11-1
- Project period: 2023 - 2026
- Project partner: Technische Universität Berlin (TUB), Institut für Bauingenieurwesen, Entwerfen und Konstruieren – Stahlbau
Steel composite structures have established themselves as an economical construction method for large bridges with spans exceeding 50 meters. Typically, composite joints are formed using headed stud anchors, which are intentionally subjected to both longitudinal and transverse loads in bridges of this type. Over the service life, the passage of individual vehicle axles results in an ultra-high-cycle loading regime with relatively small stress amplitude variations. The current DIN EN 1994-2 prescribes a characteristic Wöhler curve with a linear slope of m = 8 without a fatigue limit to describe the fatigue behavior of headed stud anchors.
Within the scope of this DFG research project at the Technical University of Munich (TUM), in collaboration with the Technical University of Berlin (TUB), an experimental and reliability-theoretically based fatigue endurance limit is being determined. Additionally, an analysis of the influence of multiaxial loading on the fatigue-loaded shear connection with headed stud anchors is being conducted. For the experimental investigations, a novel test setup is being constructed, allowing for fatigue tests of groups of up to 25 headed studs in various loading directions. Using the ultrasonic-based non-destructive testing method PAUT-Total-Focusing-Method (PAUT-TFM), the studs are examined for potential cracks at defined intervals during the tests, as it is suspected that fatigue-resistant construction can only be achieved by avoiding cracks at the notches of the stud welds. Furthermore, the results are supplemented and compared with numerical investigations using a Finite Element model based on the Concrete Damaged Plasticity (CDP) model. Finally, comparative measurements are conducted on real composite bridges to validate the obtained results.
Modular rolled girder in concrete frame bridge
- AiF-FOSTA project: IGF number 22741 N/2
- Project period: 2023 - 2025
- Project partner: Karlsruher Institut für Technologie (KIT), Stahl- und Leichtbau, Versuchsanstalt für Stahl, Holz und Steine
WiB bridges are composite bridges with rolled girders concreted in the longitudinal direction. The WiB construction method is increasingly being used in the (replacement) construction of railway overpasses. In the span range between 10 m and 30 m, this composite construction method is a proven, economical and dominant solution. The integral construction method in bridge building opens up additional economic, constructive and design potential. By eliminating wearing parts, such as bearing, joint and transition structures, as major cost drivers in construction and maintenance, life cycle costs are significantly reduced.
In this research project, the essential boundary conditions in the design of a modular WiB frame bridge will be analysed and identified and a simple, practicable and cost-effective constructive solution for the WiB frame corner will be developed. In particular, the performance capabilities in the construction, operation and dismantling phases are optimised by the planned implementation of the WiB frame bridge in modular construction, which should lead above all to a minimisation of the life cycle costs as well as the economic effects.
In close coordination with the Karlsruhe Institute of Technology (KIT), cyclic tests on scaled test specimens are being carried out at the Technical University of Munich (TUM) to investigate the joining methods of the WiB precast elements at the frame corner, as the behaviour of the precast element joints is an important component in the design of the WiB frame bridge. At KIT, large-scale static and cyclic tests as well as numerical investigations are being carried out simultaneously in order to develop a holistic picture of the load-bearing behaviour of a modular WiB frame bridge.
Method for assessing the remaining service life and determining safe operating time intervals of existing welded steel bridges
- DFG-project 506471463
- Project period: 2022 - 2025
For the assessment of existing welded steel components under cyclic loading, no probabilistically validated verification concept based on fracture mechanics exists so far. However, this is essential in order to be able to make reliable statements on the remaining service life and safe inspection intervals for the large number of historic steel structures. This is the only way to ensure the economic and safe operation of structures with correspondingly critical structural details. The existing verification based on the nominal stress concept is usually not sufficient for this purpose. In the case of bridges, various uncertainties in the input parameters such as the load history or material lead to inaccurate results. In addition, the current condition of the structure is not included in the verification. Therefore, the aim of the planned project is to develop a validated method for the determination of safe operation time intervals and remaining service life by means of crack propagation simulations. In this context, the current condition of the structure and the scatter bands of the input parameters are also to be considered. The methodology to be developed should be simple and easy to apply without the need for time-consuming crack propagation calculations. It is based on fracture mechanical analyses and is characterized by a probabilistically secured verification concept. Within the scope of the project, it will be developed exemplarily for railroad bridges. Appropriate input parameters with associated statistical distribution functions are to be defined as part of the project. These include appropriate initial crack sizes and crack propagation directions, validated material parameters and the influence of loading including possible residual stresses. In addition, relevant design details have to be transferred into idealized fracture mechanical reference models. On this basis, a general concept for older steel structures will be developed. For this purpose, fracture mechanical simulations are planned, the results of which can subsequently be transferred into correspondingly safe inspection intervals via regression analyses and probabilistic considerations. In order to validate the concept, Monte Carlo simulations will be conducted and intensive scientific work will be carried out on the safety levels and targeted level of safety. The aim of the research project is to develop a reliability-theoretical verification concept based on fracture mechanics, through which further use of existing steel structures can safely be assessed.
Seal-welded hollow boxes
- AiF-DASt-project
- Project period: 2022 - 2025
In bridge construction, non-accessible box girders represent a sustainable and resource-saving construction method due to the wide range of possible applications, the advantages in manufacturing and the possibility of dispensing with a corrosion protection layer inside the girders. However, due to the small size of the box girder, accessibility is limited and inspection of the box girders is difficult. To prevent damage prematurely, the construction method is therefore subject to particularly high requirements in terms of tightness. Due to the daily and seasonal temperature fluctuations inside the box, pressure fluctuations occur inside the box because of this tightness.
Due to the geometry, two of the longitudinal seams of seal-welded box girders can inevitably only be welded from the outside, so that due to manufacturing and economic aspects, the weld seams are usually executed as single-sided welded fillet welds. Due to the pressure fluctuations inside the box, these single-sided welded fillet welds experience additional bending stress around the longitudinal axis compared to the double-sided welds.
In the research project, this unplanned load case and the load-bearing capacity of single-sided welded fillet welds are to be examined in more detail. For this purpose, numerical investigations of the heating behavior of tightly welded box girders are carried out on the basis of weather data. From these investigations, the action required for the design can be derived. On the other hand, the load-bearing and fatigue behavior of unilaterally welded fillet welds and of the entire "tightly welded box girder" system will be investigated by means of experimental and numerical studies. The results will be used to develop a model to represent the load-bearing behavior and the resistance and can be used in a further step to develop an economical design procedure.
Longitudinally stiffened buckling fields under multiaxial loading
- AiF-DASt-project: IGF-number 20455 N/2
- Project period: 2018 - 2021
- Project partners: Institute for Construction and Design at the University of Stuttgart
During incremental launching in steel and composite bridge construction, biaxial stress states occur in the web and bottom plate, which are decisive for the dimensioning of the structural components. Significant influences on the buckling behavior in this stress state are the stress ratio σx/σz, slenderness, imperfections, the bending and torsional stiffness of the stiffeners and the type of launching bearing.
The research project will clarify the following currently open scientific questions:
- Column-like behavior of stiffened plates under compression in the transverse direction.
- Verification of the buckling check of longitudinal stiffened plates under biaxial compressive stresses
- Choice of geometric equivalent imperfection for calculation according to Theory II. Order
- Overestimation of load bearing capacity of buckling behavior under transverse loads according to DIN EN 1993-1-5 (10)
- Influence of resulting load eccentricity with different launching bearing systems (spherical bearing/rocker)
- Influence of the torsional stiffness of longitudinal stiffeners
For this purpose, a total of 12 tests will be carried out at TUM, in each of which one of the parameters will be varied. In addition, the test results of 6 buckling tests carried out as part of the "Thulba" research project are available. Based on this extensive data set, it is possible to transfer the results to individual cross-sections by means of a numerical model carefully validated on the tests. The aim of the research project is to develop improved design and dimensioning principles for buckling under biaxial stresses. In doing so, the verification concepts for a safe and economical application of the design rules according to DIN EN 1993-1-5 are to be further developed and improved in order to ensure the safety, economy and clarity of the rules in the standard. This will make the launching more attractive, benefiting SMEs in the steel construction industry and engineering companies in particular.
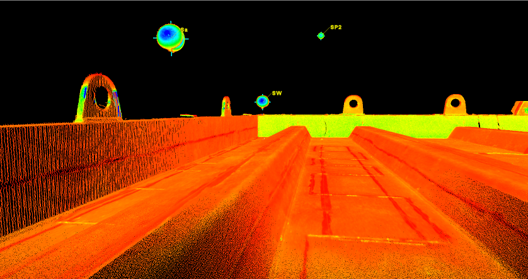
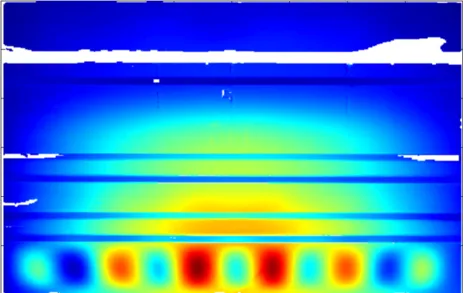
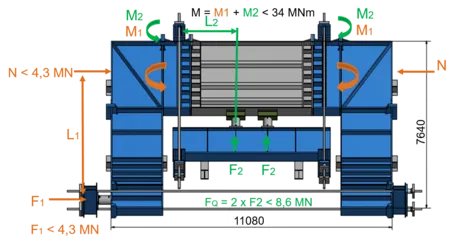
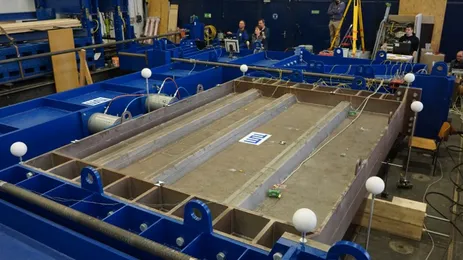
grouted joint for integral composite frame bridges suitable for hot dip galvanizing
- AiF-FOSTA-project: IGF-number 04267/17
- Project period: 2018 - 2021
- Project partner: Chair of Concrete Construction at TUM, Federal Institute for Materials Research and Testing (BAM)
Recent investigations paved the way for hot dip galvanizing (hdg) in the field of bridge constructions. The application of hdg is of special interest for composite frame bridges, as the share of integral composite frame bridges in the road and highway system has been growing over the last decades. Composite frame brdiges span up to 60m and can be built without the need of a center bearing. This results in short assembly times as well as a minimal impact on traffic. It also also provides low maintenance costs, as a transition construction or elastomeric bearings are not required.
Due to technical limitations of hot dip galvanizing, steel girders longer than 16 meters have to be divided and connected afterwards. The Chair of Metal Structures works in cooperation with the Chair of Concrete Structures of the Technical University of Munich (TUM) and the Bundesanstalt für Materialforschung und -prüfung (BAM), to develop a grouted joint connection, which meets the technical, structural and architectural requirements. In contrast to welding the segments on site or using prestressed bolt connections, the hot dip galvanization of the grouted joint remains undamaged for the whole service life time and provides a simple and robust bridge detail.
The design of the grouted connection consists of interlocking steel T-studs, diaphragms and longitudinal plates embedded in a box girder. To ensure a form- and force-locking connection, the hollow space surrounding the T-Studs is grouted with Ultra-High-Performance Fiber-Reinforced Concrete (UHPFRC). The figures show the grouted joint before and after connecting the steel segments. The diaphragms, which are closer to the T-studs, enclose the space for the grouting. The load-bearing and fatigue behavior of the joint will be investigated experimentally through tests on small-scale as well as on component tests. The results are summarized in a report and a brochure.